Lean Blog Interviews - Healthcare, Manufacturing, Business, and Leadership
Started in 2006, the ”Lean Blog Interviews” podcast, hosted by Mark Graban, brings you conversations with leading experts, authors, and thought leaders in lean manufacturing and management. As a Lean practitioner, consultant, and author, Mark Graban offers deep insights, real-world experiences, and practical tips for implementing and enhancing Lean practices across various industries. The Podcast Experience Mark Graban engages his guests in a conversational format, covering a wide array of topics related to Lean. Guests come from diverse backgrounds, including healthcare, manufacturing, and service industries, sharing their unique experiences and perspectives on Lean implementation. Core Topics Lean Principles and History: Dive into the foundational aspects of Lean, its history, and core principles. Industry Applications: Explore how Lean is applied in different industries, such as healthcare, manufacturing, and startups. Continuous Improvement: Learn about value stream mapping, process improvement, and culture change. Leadership and Management Systems: Gain insights into the Toyota Production System and related methodologies, focusing on Lean as a culture, philosophy, and management system rather than just a set of tools. Unique Features Focus on Healthcare: Mark Graban, a renowned advocate for Lean in healthcare, frequently features experts who discuss patient safety, quality improvement, and waste reduction in healthcare settings. Hear success stories and practical advice on implementing Lean in hospitals, clinics, and other healthcare organizations. Practical Advice and Real-World Examples: Guests share their experiences and insights into what works and what doesn’t in Lean implementation. Overcome common challenges and get inspired by success stories. Inclusivity and Diversity: The podcast features a range of guests from diverse backgrounds, enriching discussions and providing a comprehensive understanding of Lean’s challenges and opportunities. While we don’t talk much about Lean Six Sigma, we hope the podcast is helpful to you anyway. Why Listen? Whether you’re new to Lean or a seasoned practitioner, the ”Lean Blog Interviews” podcast is a valuable resource offering insights, tips, and inspiration for improving your organization’s performance and achieving Lean goals. With its engaging format, practical advice, and diverse range of guests, this podcast is essential for anyone interested in continuous improvement and operational excellence. Connect and Explore More Visit the blog at www.leanblog.org. For feedback, email mark@leanblog.org. Access all past episodes, show notes, and more at www.leancast.org. Subscribe to the ”Lean Blog Interviews” podcast today and join the journey toward Lean mastery and continuous improvement.
Episodes
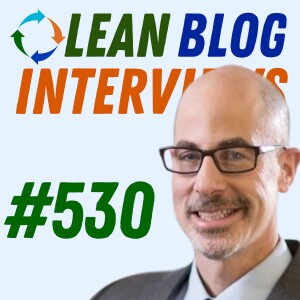
2 hours ago
2 hours ago
My guest for Episode #530 of the Lean Blog Interviews Podcast is Ken Segel, Co-Founder and Chief Relationship Officer at Value Capture.
Episode page with video and more
With over two decades of experience in healthcare improvement, Ken has been instrumental in guiding Value Capture's mission: helping healthcare organizations pursue habitual excellence by applying principles of safety, transparency, and systems thinking. In this episode, Ken shares lessons drawn from his unique and non-traditional journey--from public policy work in Washington, D.C. to transformative partnerships with industry icon Paul O'Neill and the Pittsburgh Regional Health Initiative.
Ken and I explore why world-class safety, quality, and financial performance can and must co-exist, and how starting with safety unlocks powerful learning across any organization. He reflects on how Paul O'Neill inspired leaders to set seemingly audacious goals like "zero harm"--not to punish failure, but to align people around shared purpose and continuous improvement. We also discuss the importance of creating a comprehensive operating system, one that fully integrates work systems, management systems, and improvement systems--not just Lean tools or events in isolation.
Listeners will learn why Ken believes deeply in the Shingo Principles, and why Value Capture remains the only Shingo Affiliate firm dedicated exclusively to healthcare. He also talks about the recent leadership transition at Value Capture, passing the CEO baton to longtime colleague Shanna Padgett. Whether you're a Lean healthcare leader or someone passionate about values-based leadership, this conversation offers rich insights into guiding with purpose, learning from failure, and building systems that support excellence for all.
Ken previously appeared on My Favorite Mistake (Episode 147), where he shared a powerful story about early-career lessons in leadership and systems thinking that helped shape his path into healthcare improvement.
Questions, Notes, and Highlights:
Can you share your Lean origin story?
(How did your unconventional path lead you into this work?)
What was it like working with Paul O'Neill, and how did he influence your thinking?
What was the vision and impact of the Pittsburgh Regional Health Initiative?
Why was setting a goal of zero harm so controversial--and so powerful?
How did leaders like Dr. Richard Shannon apply these principles to dramatically improve patient safety?
Where do you see progress--and continued challenges--around transparency and safety sharing in healthcare?
Why is safety such an effective entry point for broader transformation?
How do you define a "comprehensive operating system" in a healthcare context?
What's the difference between a management system and a full operating system?
How can the Shingo principles support healthcare organizations on their improvement journey?
What does it mean for Value Capture to be a Shingo Affiliate focused solely on healthcare?
What advice would you give to a health system leader who thinks they already have a Lean system in place?
Can you share the recent leadership transition news at Value Capture?
This podcast is part of the #LeanCommunicators network.
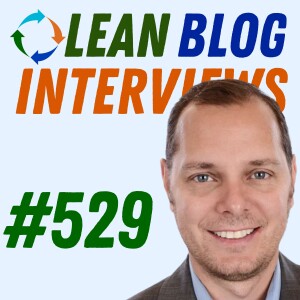
Wednesday Jun 25, 2025
Wednesday Jun 25, 2025
My guest for Episode #529 of the Lean Blog Interviews Podcast is Scott Gauvin, CEO of Macresco and co-creator of the Respect for People Roadmap.
Episode page with video, transcript, and more
With 30 years of experience leading operational transformations across sectors including biotech, pharma, agriculture, and manufacturing, Scott brings both a systems mindset and a people-first philosophy to his work. His journey into Lean began with frustration over leadership that blamed people rather than fixing systems—sparking a personal quest to better integrate continuous improvement with what he calls the “practice” of respect for people.
In this episode, Scott shares the evolution of his thinking and how it culminated in the Respect for People Roadmap, a structured learning experience designed to operationalize cultural change through nine actionable behaviors. We explore the difference between “respecting people” as an individual action and “respect for people” as a system-level design principle. Scott also challenges the common notion that respect must be earned, arguing instead that every human being is inherently worthy of it—an idea rooted in his research on Confucian influences within Toyota’s founding culture.
This conversation is a must-listen for anyone struggling to move beyond Lean tools and truly build a culture of continuous improvement grounded in human dignity. We also touch on how these ideas align with the Shingo Model, why so many transformations fail to stick, and how organizations can design systems that scale respect—without waiting for permission from the top. Check the links below to learn more and access Scott’s free “test drive” version of the Roadmap.
Questions, Notes, and Highlights:
What’s your origin story with Lean and operational excellence?
What drew you to explore the “respect for people” pillar more deeply?
How do you distinguish between “respect for people” and “respecting people”?
Why do so many interpretations of “respect” default to hierarchy or politeness?
How should leaders approach differences in how individuals define respect?
Is it a mistake to assume respect must be earned rather than given?
What are your thoughts on the phrase “better to be respected than liked”?
How do challenge, kaizen, and respect interrelate in Toyota thinking?
What did your research uncover about Confucianism’s influence on Lean?
How does the concept of “respect for people” show up in system design?
What inspired the creation of the Respect for People Roadmap?
What are the three key behavioral principles embedded in the Roadmap?
What makes this program scalable and sustainable across organizations?
Why was it important that the nine behaviors require no leader permission?
How do you respond to the idea that “respect for people” should be translated as “respect for humanity”?
Are you looking to pilot the Roadmap in healthcare settings?
What would transformation look like if it were truly resilient—not dependent on a single leader
This podcast is part of the #LeanCommunicators network.
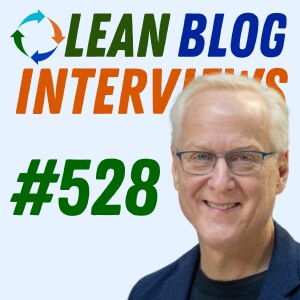
Wednesday Jun 11, 2025
Mark Reich, Former Toyota Leader on Hoshin Kanri and 'Managing on Purpose'
Wednesday Jun 11, 2025
Wednesday Jun 11, 2025
My guest for Episode #528 of the Lean Blog Interviews Podcast is Mark Reich, a Senior Lean Coach with the Lean Enterprise Institute and former Toyota leader with over two decades of experience.
Episode page with video, transcript, and more
Mark spent six years working in Japan, including helping launch the Lexus brand and later leading Hoshin Kanri strategy processes during Toyota's rapid growth in North America. He also played a pivotal role at the Toyota Supplier Support Center (TSSC), helping bring the Toyota Production System to manufacturing, healthcare, and nonprofit organizations. In our conversation, we dive into his career journey, his approach to Lean leadership, and the practical lessons behind his new book, Managing on Purpose: Using Hoshin Kanri to Develop Strategy, Align Teams, Grow Leaders, and Innovate Your Enterprise.
You can get a 25% discount on the book via LEI using the code LBIPODCAST25.
Mark shares compelling stories from his early days at Toyota, including working on the front lines of assembly, learning by doing, and his first experience pulling the andon cord. These moments shaped his appreciation for Toyota's deep respect for frontline work and its commitment to developing people. He reflects on how Toyota embeds learning and support into problem solving, where pulling the cord is seen as a learning opportunity, not a failure. That mindset became foundational for his later work, especially when managing enterprise-wide strategy through Hoshin Kanri.
We also explore what Hoshin Kanri really is--and what it isn't. Mark challenges the overemphasis on tools like the X-matrix and instead advocates for focusing on purpose, alignment, and leadership behavior. He explains how strategy deployment at Toyota was never a one-way cascade, but a dialogue grounded in humility, curiosity, and shared responsibility. Whether you're new to Hoshin or struggling to sustain it, Mark offers insights that can help any leader make strategy a living, breathing part of organizational culture.
Questions, Notes, and Highlights:
How did you end up working for Toyota, and what led you to Japan?
What was your educational background, and did you already speak Japanese before moving there?
What was your initial role at Toyota, and how did it relate to their global expansion?
Did you meet or work with John Shook during your time in Japan?
How did Toyota develop you into an industrial engineer despite your background in English writing?
What was it like working in a Toyota plant, and what did you learn from that experience?
Did you experience any early mistakes or learning moments while working the line?
How did your role evolve after leaving Japan, and how did you get involved with Hoshin Kanri in North America?
What challenges was Toyota North America facing that made Hoshin Kanri so essential?
How did you facilitate alignment and catchball between Toyota's plants and leadership teams?
How do you define Hoshin, strategy, and Hoshin Kanri?
Why do you prefer not to use the term "strategy deployment," and what's the issue with top-down-only thinking?
How do you coach executives to embrace catchball and bottom-up engagement?
How do you balance executive direction with frontline input in strategy development?
What role does psychological safety play in making Hoshin Kanri work?
How does A3 problem solving fit into the Hoshin process, and how does it help build capability?
Why is it important for executives to practice PDCA and engage in direct problem solving?
What's the difference between long-cycle and short-cycle PDCA, and how should leaders manage both?
Why does it take most organizations a couple of years to fully embed Hoshin Kanri?
What lessons do companies learn when they start with too many strategic initiatives?
Why did you choose not to include the X-matrix in your book, and what are your thoughts on its use?
What business problems does Hoshin Kanri best help organizations solve?
How can Hoshin Kanri help clarify the distinction between daily management and long-term strategic work
This podcast is part of the #LeanCommunicators network.
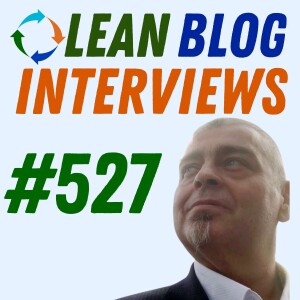
Tuesday May 13, 2025
Tuesday May 13, 2025
My guest for Episode #527 of the Lean Blog Interviews Podcast is Dave Fitzpatrick, co-founder of Zenkai Improvement Partners and a 30-year resident of Japan. Dave brings a unique perspective as a Canadian Lean practitioner who has worked extensively in both manufacturing and healthcare, guiding international leaders on immersive study experiences throughout Japan.
Episode page with video, transcript, and more
In this episode, Dave and I share details about a new collaboration we're leading together--the Lean Healthcare Accelerator Experience. This is a jointly developed series of immersive visits to high-performing organizations in Japan, designed specifically for healthcare executives who want to see Lean principles in action across both hospitals and manufacturing settings. We talk about why we're creating this experience, what makes it unique, and how cultural context, leadership behaviors, and intentional long-term commitments drive sustainable improvement--not because it's "just Japan," but because of the systems and mindsets these organizations have cultivated.
Dave shares his personal Lean journey, including how he transitioned from working in aeronautics to leading study tours for visiting professionals. He reflects on the differences between Japanese and Western companies when it comes to employee engagement, psychological safety, and respect for people. We also preview the first Accelerator trip taking place in June 2025 and discuss what makes these experiences so valuable and transformational for participants.
Whether you're in healthcare or another industry, this conversation is packed with insights about creating a culture of continuous improvement--and how a visit to Japan can accelerate your learning.
Questions, Notes, and Highlights:
Can you share your origin story--how did you first get involved with Lean, Kaizen, or the Toyota Production System?
What initially stood out to you when you began visiting Japanese manufacturing and healthcare organizations?
From your experience, what cultural factors give Japanese organizations an advantage--or do they?
How do successful Japanese companies build deep employee engagement and commitment to improvement?
What lessons can visitors take home from Japan--and why is it not just about being "Japanese"?
What are some common misconceptions people have before visiting Japan on these study experiences?
How does hierarchy or seniority in Japanese companies affect psychological safety and speaking up?
What kinds of organizations will we be visiting during the Lean Healthcare Accelerator?
What role will Reiko Kano play in these visits, and how does her expertise go beyond translation?
What's the value of including manufacturing visits in a healthcare-focused learning experience?
How do Japanese companies view improvement work in relation to headcount and job security?
Why is respect for people and time such a noticeable theme in Japanese customer service and operations?
What do you hope participants in the Lean Healthcare Accelerator take away from this experience?
This podcast is part of the #LeanCommunicators network.

Wednesday Apr 09, 2025
Leading Lean for Profitable Growth: CEO Bill Canady on Driving Business Transformation
Wednesday Apr 09, 2025
Wednesday Apr 09, 2025
My guest for Episode #526 of the Lean Blog Interviews Podcast is Bill Canady, a seasoned global business executive, U.S. Navy veteran, and current CEO of Arrowhead Engineered Products.
Bill has led over 30 operating companies and thousands of employees across the industrial and consumer products landscape. Formerly CEO of OTC Industrial Technologies, he helped drive impressive growth-boosting revenues by 43% and earnings by 78%.
Bill is also the author of The 80/20 CEO and the upcoming From Panic to Profit, and he's a vocal advocate for using Lean and the 80/20 principle as complementary tools for transformation.
Join Bill for a live Q&A webinar on April 23rd via KaiNexus!
We discuss Bill’s personal Lean journey, which began with Six Sigma and evolved into a deep appreciation for the power of Lean and continuous improvement. He shares how daily management, Kaizen events, and a focus on flow became core to his leadership toolkit—not just on the shop floor but also across the “carpeted” functions like order-to-cash and sales. As CEO, Bill doesn’t just support Lean; he expects it. He talks candidly about making continuous improvement a condition of employment, not through fear, but by creating a culture where people feel safe, engaged, and energized by problem-solving.
You’ll hear Bill’s insights on applying Lean as a strategic enabler for profitable growth—not just a cost-cutting tool. He explains how the 80/20 principle helps companies focus their improvement energy on what really matters and how Lean helps teams sustain those improvements. He also shares real-world lessons on leadership, cultural alignment, and navigating resistance to change—especially among those clinging to old firefighting habits.
Whether you’re a Lean practitioner, an executive, or someone aspiring to lead, this conversation is packed with practical wisdom. Bill offers a compelling blueprint for how to lead with humility, clarity, and purpose—using Lean and the 80/20 mindset to build resilient, high-performing organizations.
Questions, Notes, and Highlights:
Can you share your origin story with continuous improvement and Lean?
What was the context in which you were first introduced to these methodologies?
How did your role evolve from operations into broader P&L responsibility?
How did your perspective on Lean shift when you became a CEO?
What role does daily management play in sustaining operational excellence?
How do you apply Lean principles outside the factory floor—especially in “carpet land”?
As a CEO, how do you strike the balance between solving problems yourself and enabling others to be problem solvers?
How do you respond when leaders or team members resist Lean thinking or default to old firefighting habits?
What does it mean to make Lean a “condition of employment,” and how do you introduce that mindset?
How do you ensure people understand Lean isn’t about layoffs, but about redeployment and growth?
How do you connect Lean initiatives with business growth, not just cost reduction?
Do you have an example of how improving quality or delivery led directly to business growth or profitability?
What inspired you to write your first book, The 80/20 CEO?
Why are the first 100 days so critical for a new leader?
How does the 80/20 principle help leaders prioritize improvement efforts?
What’s the relationship between 80/20 analysis and Lean execution in your approach?
What can we do to help more CEOs understand and embrace Lean as a strategic business system?
How can companies start building momentum with Lean—even if they’re just getting started?
What’s the focus of your new book From Panic to Profit, and how does it expand on your first?
This podcast is part of the #LeanCommunicators network.

Wednesday Mar 19, 2025
From Noise to Knowledge: Embracing Data-Driven Leadership - Christopher R. Chapman
Wednesday Mar 19, 2025
Wednesday Mar 19, 2025
My guest for Episode #525 of the Lean Blog Interviews Podcast is Christopher R. Chapman. He's an experienced agile coach and consultant with a background in software development and agile transformation.
Episode page with video, transcript, and more
Since founding Derailleur Consulting in 2010, he has guided teams and leaders in adopting agile frameworks like Scrum and Kanban while integrating applied systems thinking inspired by Deming and other thought leaders.
Christopher is also known for cultivating communities through initiatives such as #SystemsThinkingTO and for sharing his insights in his popular Substack newsletter, The Digestible Deming.
In this episode, Chris and I discussed our upcoming collaborative workshops--"From Noise to Knowledge, Executive Leadership Through Data Driven Insight"--scheduled for
May 13 in Toronto and
June 17 in Cincinnati.
We highlighted how the sessions will blend experiential learning, such as the Red Bead Experiment, with practical tools like process behavior charts to help leaders decode variation and improve decision-making. The conversation emphasized the Deming philosophy as a core framework, exploring how leadership behaviors and systemic practices directly impact team performance and overall organizational quality. We also noted the engaging social aspect of the workshops, mentioning optional outings to local MLB baseball games as an opportunity for continued dialogue.
The discussion then shifted to our personal journeys with continuous improvement, agile methodologies, and the evolution of leadership roles. Chris shared insights from his transition from software development to coaching senior management, focusing on moving beyond traditional, isolated team interventions toward a holistic, systems-oriented approach. We both underlined the need for leadership to embrace a mindset shift--recognizing that issues within teams often reflect broader organizational constraints. We also debated common pitfalls, such as misinterpreting data due to superficial analyses, and argued for using robust, statistical tools to establish meaningful insights, setting the stage for transformative change in management practices.
Questions, Notes, and Highlights:
How do Deming's principles transform executive leadership and team performance?
What key insights does the Red Bead Experiment offer for practical improvement?
In what ways do process behavior charts enhance decision-making in complex systems?
How can agile methodologies and Deming's philosophy be integrated effectively?
What systemic issues underlie team challenges, and how should leadership address them?
How can statistical process control complement traditional metrics in agile environments?
What strategies enable leaders to shift from reactive problem-solving to proactive system improvement?
How do extrinsic incentives impact collaboration and quality within teams?
What methods best embed systems thinking into agile practices?
How can workshop formats foster lasting changes in leadership mindsets?
This podcast is part of the #LeanCommunicators network.

Wednesday Mar 12, 2025
John Willis on Deming's Journey to Profound Knowledge in IT & DevOps
Wednesday Mar 12, 2025
Wednesday Mar 12, 2025
My guest for Episode #524 of the Lean Blog Interviews Podcast is John Willis, an accomplished IT management expert with over 45 years of experience. His extensive body of work includes contributions to Deming's Journey to Profound Knowledge and co-authoring The DevOps Handbook.
See video, transcript, and more
Hosts a podcast that I was recently on, "Profound."
John focuses his current research on DevOps, DevSecOps, IT risk, modern governance, and audit compliance. Over the course of his career, he has sold companies to Docker and Dell, and he played a foundational role at Opscode (now Chef).
In addition, John founded Gulf Breeze Software, an award-winning IBM business partner recognized for its successful deployment of Tivoli technology for enterprise clients. He has authored six IBM Redbooks on enterprise systems management and served as the founder and chief architect of Chain Bridge Systems. Altogether, John has written more than 11 books and launched over 10 startups, cementing his reputation as a significant innovator in the IT industry.
In this episode, the discussion navigates the intersection of lean principles, agile methodologies, and Deming's philosophies as they apply to modern IT and operations. John delves into how systems thinking, profound knowledge, and psychological safety underpin effective incident management and cybersecurity practices. The conversation explores practical challenges and the proactive strategies necessary for integrating legacy improvement methods with today's cloud innovations and infrastructure as code.
Throughout the episode, John examines the real-world application of these timeless principles, offering listeners actionable insights into continuous improvement and risk management. He highlights the importance of questioning established norms and embracing complexity to drive operational excellence, providing a compelling roadmap for navigating the evolving digital landscape.
Questions, Notes, and Highlights:
Could you share your origin story regarding Lean and continuous improvement--specifically, what you learned during your early years at Exxon?
How have you seen Deming's principle of eliminating fear put into practice in IT and entrepreneurial settings?
Is the phenomenon you described established fact or more of a hypothesis?
How can we confirm or measure the validity of that knowledge?
Why do you consider cyber terrorism one of today's most significant threats?
This podcast is part of the #LeanCommunicators network.

Thursday Feb 20, 2025
Innovating Patient Safety: Mike Eisenberg Discusses Healthcare Technology and Trust
Thursday Feb 20, 2025
Thursday Feb 20, 2025
My guest for Episode #523 of the Lean Blog Interviews Podcast is Mike Eisenberg. He's been a filmmaker since 2010 with his production company, Tall Tale Productions, after completing his B.A. in Journalism at Marietta College in Ohio.
Episode page with video, transcript, and more
Mike’s father, Dr. John Eisenberg, was a leader in national patient safety efforts as the director of the Agency for Healthcare Research & Quality (AHRQ) until his passing in 2002. His legacy is prevalent throughout Mike’s presentation, as well as his approach.
His new documentary, released last September, is titled “The Pitch: Patient Safety's Next Generation.”
He previously joined us in Episode #329, where we discussed his film "To Err is Human."
In 2006, Mike was drafted by the Cleveland Indians in the MLB Draft and played 3 seasons of professional baseball before beginning his filmmaking career. He now speaks at hospitals, universities, and conferences, where his insight provides a new perspective on a problem that persists across the globe.
In today's episode, we explore the evolution of patient safety and the transformative role of technology in healthcare. The conversation dives into how innovations—from advanced command centers to cutting-edge virtual reality and AI applications—are redefining how hospitals prevent and respond to medical errors. The discussion challenges the conventional blame-and-shame approach and instead highlights the importance of building systems that foster trust and resilience among healthcare professionals and patients alike.
We also examine the nuances of integrating technology into complex healthcare environments, discussing how effective communication, standardized protocols, and smart design can work together to minimize human error. Drawing insightful parallels with industries like aviation, the episode offers a fresh perspective on the critical need for systemic improvements and the potential for new technological solutions to drive the next generation of patient safety.
Questions, Notes, and Highlights:
How is technology transforming patient safety in healthcare?
What role do advanced command centers, virtual reality, and AI play in preventing medical errors?
How can healthcare shift away from a blame-and-shame culture?
What strategies build trust and resilience among healthcare professionals and patients?
How do effective communication, standardized protocols, and smart design minimize human error?
What lessons can be learned from the aviation industry regarding safety and error management?
What challenges arise when integrating technology into complex healthcare environments?
How can innovation drive the next generation of patient safety?
This podcast is part of the #LeanCommunicators network.

Thursday Feb 13, 2025
Thursday Feb 13, 2025
Episode page with video, transcript, and more
My guest for Episode #522 of the Lean Blog Interviews Podcast is Jacquie Maupin.
She joins the podcast to discuss her upcoming workshop at the Healthcare Systems Process Improvement Conference (HSPI) hosted by the Society for Health Systems. She and her co-presenter, Lauren Todd from HCA Healthcare, will lead a session titled "From Analysis to Action: Bridging the Gap with Effective Presentations" on February 19.
This interactive workshop is designed to help attendees sharpen their communication skills, structure data-driven narratives, and effectively engage executives and stakeholders. Whether you're attending this year or considering next year's event, this conversation offers valuable insights into the intersection of Lean, process improvement, and communication.
In this episode, we discuss how journalism and communication skills can enhance Lean and process improvement efforts. Jacquie shares how her background in journalism and military leadership shaped her approach to problem-solving, stakeholder engagement, and storytelling in the world of healthcare improvement. We explore the parallels between investigative reporting and Lean methodology—how asking the right questions, structuring information effectively, and communicating insights clearly can drive meaningful change.
We also dive into Jacquie's upcoming workshop, where she and her co-presenter, Lauren Todd, will guide attendees through strategies for tailoring presentations to different audiences, crafting compelling data-driven narratives, and influencing decision-making. Whether you're attending this year or looking for ways to elevate your communication skills in process improvement, this episode is packed with valuable lessons.
Questions, Notes, and Highlights:
Can you share your Lean origin story and career path?
How did your background in journalism and the military shape your approach to process improvement?
What sparked your interest in healthcare and led you to Georgetown University Hospital?
What were some of the most impactful projects you worked on at Georgetown?
How does process mapping help break down silos and improve collaboration?
What journalism skills translate well to process improvement and Lean work?
How do you approach communicating with executives to ensure your message is understood?
What challenges have you faced in presenting Lean concepts to different audiences?
How can process improvement teams better tell their success stories and demonstrate value?
What insights will attendees gain from your upcoming workshop at the Healthcare Systems Process Improvement Conference?
![Gemba Claus is Comin’ to Town! [Song]](https://pbcdn1.podbean.com/imglogo/ep-logo/pbblog4956472/LEAN_Blog_Podcast_and_Audio_Covers_Mark_Graban_Nov_2022_4_abg13_300x300.jpg)
Friday Dec 20, 2024
Gemba Claus is Comin’ to Town! [Song]
Friday Dec 20, 2024
Friday Dec 20, 2024
Here's a musical holiday treat for my regular Lean Blog readers and podcast listeners, a song parody, originally released in 2009... remastered a bit in 2022.
https://www.leanblog.org/2022/12/gemba-claus-comin-town-song/
Gemba Claus is Comin' to Town
Lyrics by Mark GrabanPerformance by Steve Sholtes
Oh, you'd better watch outYou'd better kaizenYou'd better not pout, I'm tellin' ya thenGemba Claus is comin' to town
He's making a listJust checking it onceDoin' it twice would waste a whole bunchGemba Clause is comin' to town
He sees you when you're waitin'He knows when your work flowsHe knows if changeovers are too longSo do SMED for goodness sake
Oh, you'd watch outYou'd better not pauseYou'd better not poutFind the real root causeGemba Claus is comin' to Town!
For voiceover work, music, or more, you can contact Steve via his website, www.stevesholtes.com.
Merry Christmas and Happy Holidays!
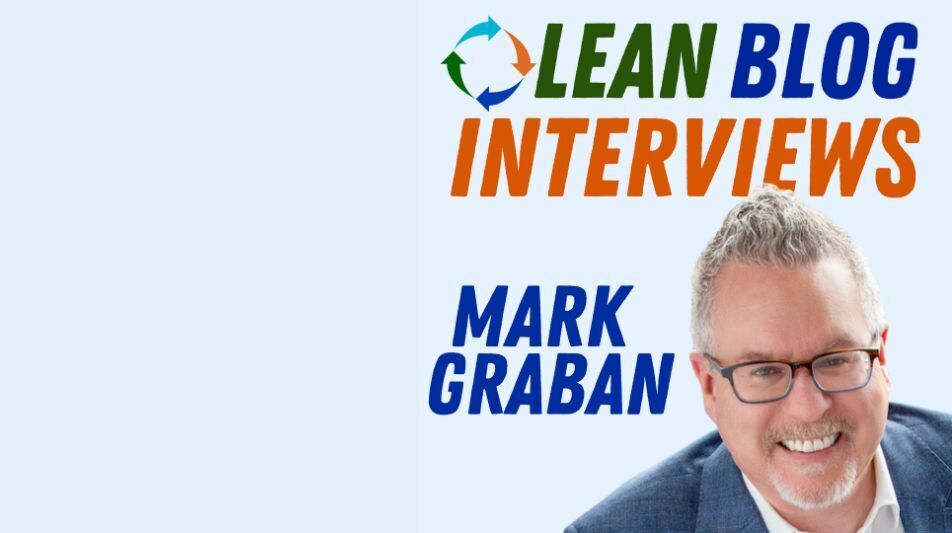
About Mark Graban
Mark Graban is an author, speaker, and consultant, whose latest book, The Mistakes That Make Us: Cultivating a Culture of Learning and Innovation, is available now.
He is also the author of the award-winning book Lean Hospitals: Improving Quality, Patient Safety, and Employee Engagement and others, including Measures of Success: React Less, Lead Better, Improve More.
He serves as a consultant through his company, Constancy, Inc, and is also a Senior Advisor for the technology company KaiNexus.
Mark hosts podcasts, including “Lean Blog Interviews” and “My Favorite Mistake.”
Education: B.S. in Industrial Engineering from Northwestern University; M.S. in Mechanical Engineering, and M.B.A. from the Massachusetts Institute of Technology’s Leaders for Global Operations Program.