Lean Blog Interviews - Healthcare, Manufacturing, Business, and Leadership
Started in 2006, the ”Lean Blog Interviews” podcast, hosted by Mark Graban, brings you conversations with leading experts, authors, and thought leaders in lean manufacturing and management. As a Lean practitioner, consultant, and author, Mark Graban offers deep insights, real-world experiences, and practical tips for implementing and enhancing Lean practices across various industries. The Podcast Experience Mark Graban engages his guests in a conversational format, covering a wide array of topics related to Lean. Guests come from diverse backgrounds, including healthcare, manufacturing, and service industries, sharing their unique experiences and perspectives on Lean implementation. Core Topics Lean Principles and History: Dive into the foundational aspects of Lean, its history, and core principles. Industry Applications: Explore how Lean is applied in different industries, such as healthcare, manufacturing, and startups. Continuous Improvement: Learn about value stream mapping, process improvement, and culture change. Leadership and Management Systems: Gain insights into the Toyota Production System and related methodologies, focusing on Lean as a culture, philosophy, and management system rather than just a set of tools. Unique Features Focus on Healthcare: Mark Graban, a renowned advocate for Lean in healthcare, frequently features experts who discuss patient safety, quality improvement, and waste reduction in healthcare settings. Hear success stories and practical advice on implementing Lean in hospitals, clinics, and other healthcare organizations. Practical Advice and Real-World Examples: Guests share their experiences and insights into what works and what doesn’t in Lean implementation. Overcome common challenges and get inspired by success stories. Inclusivity and Diversity: The podcast features a range of guests from diverse backgrounds, enriching discussions and providing a comprehensive understanding of Lean’s challenges and opportunities. While we don’t talk much about Lean Six Sigma, we hope the podcast is helpful to you anyway. Why Listen? Whether you’re new to Lean or a seasoned practitioner, the ”Lean Blog Interviews” podcast is a valuable resource offering insights, tips, and inspiration for improving your organization’s performance and achieving Lean goals. With its engaging format, practical advice, and diverse range of guests, this podcast is essential for anyone interested in continuous improvement and operational excellence. Connect and Explore More Visit the blog at www.leanblog.org. For feedback, email mark@leanblog.org. Access all past episodes, show notes, and more at www.leancast.org. Subscribe to the ”Lean Blog Interviews” podcast today and join the journey toward Lean mastery and continuous improvement.
Episodes
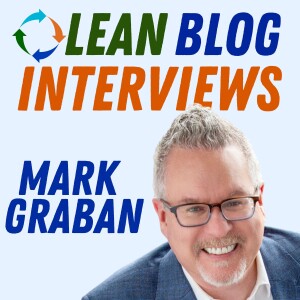
Tuesday Aug 02, 2022
Luke Szymer on Agile, Testing Hypotheses, and Process Behavior Charts
Tuesday Aug 02, 2022
Tuesday Aug 02, 2022
Founder of “Launch Tomorrow.”
Episode page with transcript, video, and more
My guest for Episode #452 of the Lean Blog Interviews Podcast is Luke Szyrmer. He's the founder of “Launch Tomorrow.” He helps new technology products get to market faster (even remotely).
Luke is the author of the books Align Remotely: How to achieve together, when everyone is working from home and Launch Tomorrow: Take Your Product, Startup, or Business From Idea to Launch in One Day.
He's the host of the highly rated “Managing Remote Teams” podcast. He comes from a product management background and has a BA in Economics and English from the University of Pennsylvania.
He's joining us on the podcast from Poland.
Today, we discuss topics and questions including:
Background question — How did you get introduced to Agile, Lean Startup, things like that?
“Fuzzy side of innovation”?? — time wasted 20-30 years ago?
Doing the wrong things righter?
Tampering – and increasing variation
Processes for creating software?
When you were reading about “Lean Manufacturing”? How does that resonate with? How does that relate to you and your work?
How easy is it to estimate “story points”?
Lean Thinking – batch vs flow… physical flow vs. work flow — Adaptations to the flow of software?
Takt time – how to translate this in terms of required software, requirements, points
How did you learn about Process Behavior Charts?
Why did that resonate with you?
How do you incorporate PBCs into your work?
Counting physical products vs. story points (something more esoteric)?
Landing pages – product or service that doesn't exist yet
What to test BEFORE a landing page?
How to make a good decision with limited data points?
What's so powerful about testing an idea as a hypothesis?
The podcast is sponsored by Stiles Associates, now in their 30th year of business. They are the go-to Lean recruiting firm serving the manufacturing, private equity, and healthcare industries. Learn more.
This podcast is part of the #LeanCommunicators network.
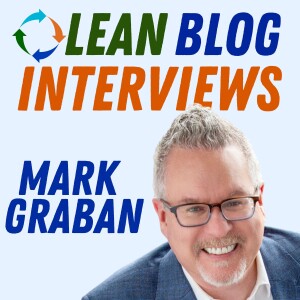
Tuesday Jul 26, 2022
Tuesday Jul 26, 2022
Episode page: https://leanblog.org/451
My guest for Episode #451 of the Lean Blog Interviews Podcast is Dr. Alan G. Robinson. He specializes in managing ideas, building high-performance organizations, creativity, innovation, quality, and lean production. He is the co-author of 13 books, many of which have been translated into more than twenty-five languages.
Dr. Robinson is on the faculty of the Isenberg School of Management at the University of Massachusetts. He received his Ph.D. in applied mathematics from the Whiting School of Engineering at Johns Hopkins University, and a B.A. and M.A. in mathematics from the University of Cambridge.
He has served on the Board of Examiners of the United States' Malcolm Baldrige National Quality Award and on the Board of Examiners for the Shingo Prizes for Excellence in Manufacturing.
He's a returning guest (Episode 217) – talked about one of his previous books (co-authored with Dean Schroeder) — The Idea-Driven Organization.
His bestselling book, Ideas Are Free, co-authored with Schroeder, was based on a global study of more than 150 organizations in 17 countries. It describes how the best companies go about getting large numbers of ideas from their front-line employees, and the competitive advantages they gain from this.
His new book, available now, also co-authored with Schroeder is Practical Innovation in Government: How Front-Line Leaders Are Transforming Public-Sector Organizations.
Today, we discuss topics and questions including:
As we've learned from you previously… “Roughly 80 percent of any organization's improvement potential lies in front-line ideas.” — Potential?
Continuous Improvement vs Innovation? Used to draw a distinction
The Tesla factory doesn't have the continuous improvement culture of NUMMI?
How much progress have you seen in terms of executives understanding the power of engaging everybody in bring forward and implementing ideas?
Alan's first book was with Shingo — “mass creativity”
UMass Memorial Health — 100,000 ideas and your role helping them?
Tell us about the new book — what prompted you and Dean to write this for this audience? What prompted the research?
Educating / influencing elected leaders vs. career government employees
The role of front-line leaders vs. senior leaders vs. elected officials?
Non-partisan – almost 50/50 from their research party wise
The phrase “practical innovation”?
Does adopting these practices mean we are “running government like a business”??
Adoption at local (including schools), state, or federal levels?
Does “practical innovation” get past pointing simply to budgets as a barrier?
Demanding cost savings or ROI is a kiss of death for improvement?
1841 — Original article that invented cost/benefit analysis… “only useful for the simplest…”
“Why cost/benefit analysis is stupid“
Would we expect government in Japan to be a leader in Kaizen?
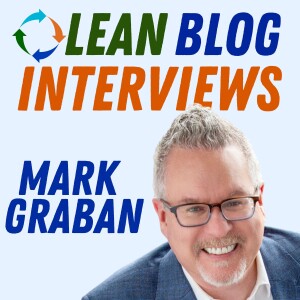
Tuesday Jul 12, 2022
Torbjorn Netland, PhD on Company Production Systems, Lean & Technology, and More
Tuesday Jul 12, 2022
Tuesday Jul 12, 2022
Episode page: https://leanblog.org/450
My guest for Episode #450 of the Lean Blog Interviews Podcast is Professor Torbjorn Netland, Ph.D.
Tor is the chair of production and operations management in the department of management, technology and economics at ETH Zurich in Switzerland.
He is a member of the World Economic Forum's Global Future Council on Advanced Manufacturing and Value Chains and a Fellow of the European Academy for Industrial Management.
His award-winning research on managing performance improvement appears in leading scientific journals such as Management Science, MIT Sloan Management Review, Journal of Operations Management, and more.
Tor is a recognized thought-leader in operational excellence (including lean) and is the recipient of two Shingo Research Awards and numerous teaching awards.
His blogs at www.better-operations.com.
Like my recent guest, Dr. Lisa Yerian (ep 449), Tor is going to be one of the keynote speakers at the 2022 AME Conference, being held in Dallas — Oct 17 to 20. I'll be there and I hope you will be too.
Today, we discuss topics and questions including:
Tor, what is the topic of your keynote talk on the AME theme of “Embrace Disruption”?
Tell us your thoughts on the role of new technologies in Lean?
Not just emulating Toyota of the 1960s
Lessons learned about bringing new ideas to people?
The dream of the lights-out factory has been haunting us for a while now – GM CEO Roger Smith in the 1980s and in more recent years Elon Musk at Tesla… is that still a dream? Is it a dystopian nightmare? Or something in between?
How did you first get interested in Lean and Operational Excellence?
Dogma vs practical realities – Buffers? Inspection?
Last year, you blogged about the confusion around “what is Lean?” How do you define Lean and what's the most common confusion?
Different views of researchers?
How do you describe the role of company-specific production systems?
Difference in having YOUR production system vs. just a name?
“If you like heated debates, start a discussion thread on the definition of lean on LinkedIn.”
Another heated debate — Lean is not TPS? Goes beyond TPS?
Tell us why it's wrong to blame JIT for pandemic-era supply chain problems…
You have a textbook, written with Michel Baudin, coming out — tell us about that?
The podcast is sponsored by Stiles Associates, now in their 30th year of business. They are the go-to Lean recruiting firm serving the manufacturing, private equity, and healthcare industries. Learn more.
This podcast is part of the #LeanCommunicators network.
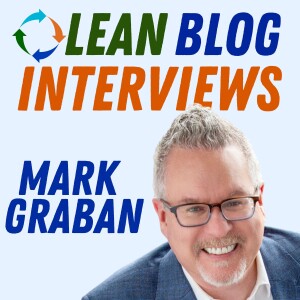
Tuesday Jun 28, 2022
Tuesday Jun 28, 2022
Chief Improvement Officer at the Cleveland Clinic
Episode page
My guest for Episode #449 of the Lean Blog Interviews Podcast is Lisa Yerian, MD.
She joined Cleveland Clinic in anatomic pathology in 2004, and has held several pathology and enterprise leadership positions. After 10 years serving as Medical Director of Continuous Improvement, Dr. Yerian was named Cleveland Clinic's first Chief Improvement Officer of Continuous Improvement in December 2019.
She's going to be one of the keynote speakers at the 2022 AME Conference, being held in Dallas — Oct 17 to 20. I'll be there and I hope you will be too.
Lisa was previously a guest here in Episode 282 back in 2017. Also joining that for that episode was our friend and her colleague, Nate Hurle.
Today, we discuss topics and questions including:
Remembering Nate Hurle (my blog post)
My last podcast with him (episode 404), Nate talked about how the CCIM and your continuous improvement work was helping with Covid testing, treatment, and vaccination… new processes.
As you shared recently at the Catalysis Lean Healthcare Transformation Summit, how did your Lean management system get you through Covid?
Daily management system
Tiered daily huddles
Problem solving systems
“Covid put that system to the test”
Adaptations were required — learned how to make changes to the standard work in hours, not weeks
Urgency – had to work past the old expectation that it takes 3 months to solve problems
The Cleveland Clinic journey
2006: project-based work and some basic tools
2012: deliberately focused on building culture
Started a “culture of improvement” A3
Defined current state, future state — and the gap
Challenge: perception that we're already doing well enough
Little Red Book of Selling (a book Nate loved)
Culture of excellence – “Not getting better fast enough”
A3 problem solving
“Having a piece of paper is a way to de-escalate…”
Building on a culture of patients first
Lisa's appearance with me on the Habitual Excellence podcast
Good enough, world class, vs. aiming for zero harm?
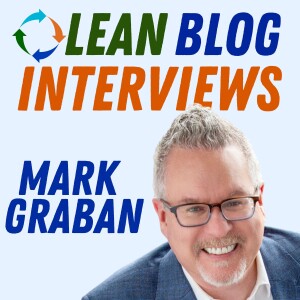
Tuesday Jun 21, 2022
Tuesday Jun 21, 2022
Episode page, video, transcript, and more
My guest for Episode #448 of the Lean Blog Interviews Podcast is Rich Sheridan, co-founder, CEO and “Chief Storyteller” of Menlo Innovations, a software and IT consulting firm that has earned numerous awards and press coverage for its innovative and positive workplace culture.
He's a returning guest from Episode 189 back in 2014 — the same year that I had a chance to visit the Menlo Innovations office.
We talked then about his first book Joy, Inc.: How We Built a Workplace People Love.
His latest book, published in 2019, is Chief Joy Officer: How Great Leaders Elevate Human Energy and Eliminate Fear.
Rich is giving a keynote talk, “Lead With Joy and Watch Your Team Fly!”, at the Michigan Lean Consortium annual conference, being held August 10-11 in Traverse City. I'll be there and I hope you'll join us.
Today, we discuss topics and questions including:
For those who didn't hear the first episode, how would you summarize “The Menlo Way”? And how has “the Menlo Way” evolved over the past 8 years?
Why is “eliminating fear” so important and what drains joy from the workplace?
“Tired programmers make bad software”
Sustainable work pace
Paired work – Erika and Lisa
Individual performance reviews?
“We've eliminated bosses” — nobody to review you, the team gives feedback, develops growth plan
“Let's run the experiment”
Toyota talks about the need for humble leaders — why is humility such an important trait? Do you hire for humility or try to screen out those without much humility?
No longer say “we hire for culture fit”
“Not an interview, an audition”
Leadership lessons from the pandemic– 4 blog posts
In “Chief Joy Officer” you write about the proverbial “mask” that leaders feel pressured to wear… masking how we really feel. Were you able to be your authentic whole self at work, fears and all, during the early stages of the pandemic?
“Scared and panicked” – was it OK to share that with the team?
“They're all adapting” – as a result of everything we've been doing for 19 years
The podcast is sponsored by Stiles Associates, now in their 30th year of business. They are the go-to Lean recruiting firm serving the manufacturing, private equity, and healthcare industries. Learn more.
This podcast is part of the #LeanCommunicators network.
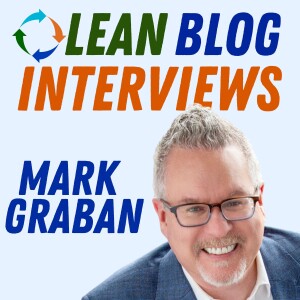
Wednesday Jun 08, 2022
Just the Lean Talk 2 -- Mark Graban & Jamie Flinchbaugh Discuss Lean Supply Chains
Wednesday Jun 08, 2022
Wednesday Jun 08, 2022
As I did two weeks ago, when Jamie Flinchbaugh and I talked about “Lean 101” training (and should you skip it), I'm sharing another episode (as a “bonus” episode in the “Lean Blog Interviews” podcast series), a “just the Lean talk” discussion.
This comes from Episode #27 where we started the episode by taking a deep dive into coffee (making it and drinking it at home) instead of talking whiskey. We were recording in the morning, so whiskey wasn't appropriate. The weather was nice, so Jamie was sitting outside, so we get to hear some birds in his background.
Again, we know many of you don't care about the whiskey talk (or coffee talk), but Jamie suggested sharing this segment where we talked about Lean in relation to inventory and supply chains. This is from May of 2021, but we think it's still relevant. If you want to hear coffee talk, listen to or watch the whole version here.
Our inventory talk includes a news story about 10 million bourbon barrels that are “resting” in inventory. But it's barely whiskey talk. We talk more about the supposed “death of Just In Time.” Ugh.
As I said last time, Jamie Flinchbaugh and I started a podcast series just over three years ago called “Lean Whiskey.” It's a very conversational format and we've enjoyed doing it (and if anybody likes listening, then even better!).
Links From the Show (about Lean):
10 Million bourbon barrels resting – too much or not enough?
The Wall Street Journey's misinformed piece on JIT, Jeff Liker on JIT, Dr. Jonathan Byrnes on supply chain shockwaves, and Dr. Byrnes as a guest Mark's LeanBlog podcast
MIT's The Beer Game, system dynamics and accumulators and delays, and supply and demand
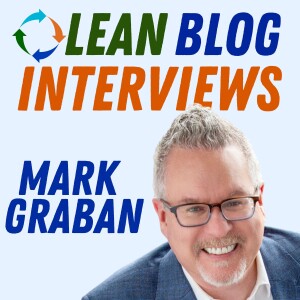
Tuesday May 24, 2022
Skip the Lean 101 Training? Mark Graban and Jamie Flinchbaugh
Tuesday May 24, 2022
Tuesday May 24, 2022
This is a "bonus" episode where Mark and Jamie talk about "Lean 101" training -- experiences, lessons learned, tips, and more.
This is the "just the Lean" part of Episode #33 of our "Lean Whiskey" podcast. We realize some of you might not care about the whiskey talk or you just don't want to hear that at all. But, the Lean discussion is pretty good, so here it is.
If you're interested in Lean Whiskey, it's quite likely that you can subscribe anywhere you are listening to this post.
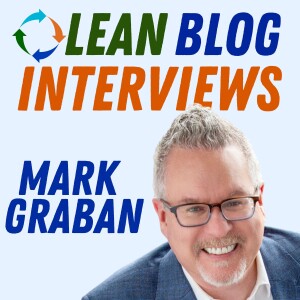
Tuesday May 10, 2022
Lauren Hisey on Bridging the Gap Between People, Process, and Technology
Tuesday May 10, 2022
Tuesday May 10, 2022
Episode page: https://leanblog.org/447
My guest for Episode #447 of the Lean Blog Interviews Podcast is Lauren Hisey.
Lauren is a Continuous Business Process Improvement consultant, coach, trainer, and speaker. She specializes in helping business owners and leaders from mid-size organizations uncover and solve their business problems with Continuous Business Process Improvement (Lean, Six Sigma, etc.). She helps your business and organization become simpler… faster… BETTER.
Today, we discuss topics and questions including:
Why is it important not to jump to solutions with technology (Robotic Process Automation, AI, Machine Learning, or the new Hyper automation)?
What is RPA?
What do you mean by “digital transformation”?
Bridging the gap – people, process, and technology
Don't automate a bad process
Why should you start with Value Stream mapping and then process mapping the current state and future state?
VSM vs. process maps? Differences?
Current state observation vs. future state creation?
Virtual suggestion box situation – technology adoption?
Virtual Gemba walks?
Why are Gemba walks so important with understanding the current state and then the future state?
Putting two things together — Lean transformation and digital transformation?
The podcast is sponsored by Stiles Associates, now in their 30th year of business. They are the go-to Lean recruiting firm serving the manufacturing, private equity, and healthcare industries. Learn more.
This podcast is part of the #LeanCommunicators network.
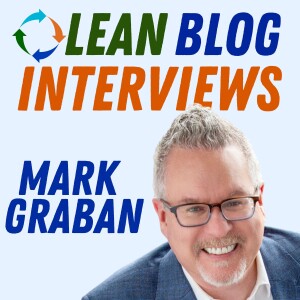
Tuesday Apr 26, 2022
Sumitra Vig on Lean & Quality: First Time Right or Next Time Right?
Tuesday Apr 26, 2022
Tuesday Apr 26, 2022
Partner with Svakarma Advisory, LLP, based in Mumbai India.
Episode page: https://leanblog.org/446
My guest for Episode #446 of the Lean Blog Interviews Podcast is Sumitra Vig. She is a partner with her advisory firm Svakarma Advisory, LLP, based in Mumbai India.
She is a customer experience specialist, an ASQ (American Society for Quality) Certified Manager of Quality & Organizational Excellence, and a master trainer & retail banker with years of hands-on international experience in Asia, Europe, Middle East, and Africa.
Sumitra has designed & conducted successful training programs, mentored employees & created an impact across continents
Today, we discuss topics and questions including:
How did you get introduced to Quality?
First time right / first time quality from a customer lens — What is this?
Does this mean “no mistakes”? What do we learn from mistakes?
Does “first time right” put too much pressure on people?
How can we design the product or service in a way that ALLOWS first time right?
Design thinking — what does the customer really want?
Measures — Problems vs reported problems — how to handle unreported problems?
Customer is king? The employee is really king to then deliver a transformational experience??
The 5 Toyota Precepts
The book Atomic Habits
Women in Lean – Our Table group on LinkedIn
Has a master class available online on First Time Right
Working with a foundation – mobile hospital for villages, remote Himalaya
The podcast is sponsored by Stiles Associates, now in their 30th year of business. They are the go-to Lean recruiting firm serving the manufacturing, private equity, and healthcare industries. Learn more.
This podcast is part of the #LeanCommunicators network.
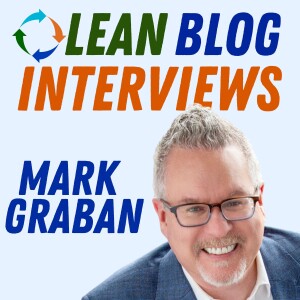
Wednesday Apr 13, 2022
Michael Parent on ”The Lean Innovation Cycle” -- Human-Centered Design and More
Wednesday Apr 13, 2022
Wednesday Apr 13, 2022
Consultant and author of "The Lean Innovation Cycle"
Episode page: https://leanblog.org/445
My guest for Episode #445 of the Lean Blog Interviews Podcast is Michael Parent. He is the Managing Director of Michael Parent Consulting Services and a Lean Six Sigma Black Belt with AAA Auto Club Group in Michigan.
He has written a new book titled The Lean Innovation Cycle: A Multi-Disciplinary Framework for Designing Value with Lean and Human-Centered Design.
Today, we're going to take a dive deep into topics that augment both the Lean and Human Centered Design frameworks.
Today, we discuss topics and questions including:
How about an Operational Definition: What is Human Centered Design?
Tools — but more than the tools
Design something… empathize with the end user
“Transparency is a good thing”
Design thinking (prototyping?) vs. human-centered design??
Observing people vs. asking them about needs as customers?
Converging toward a design?
What made you interested in exploring Human Centered Design?
What value does Human Centered Design offer for Lean, Six Sigma, and continuous improvement? Methodology, being an experimentalist
Customer journey vs. VSM? Or Customer Journey VSM hybrid?
What is the Kano model?
The podcast is sponsored by Stiles Associates, now in their 30th year of business. They are the go-to Lean recruiting firm serving the manufacturing, private equity, and healthcare industries. Learn more.
This podcast is part of the #LeanCommunicators network.
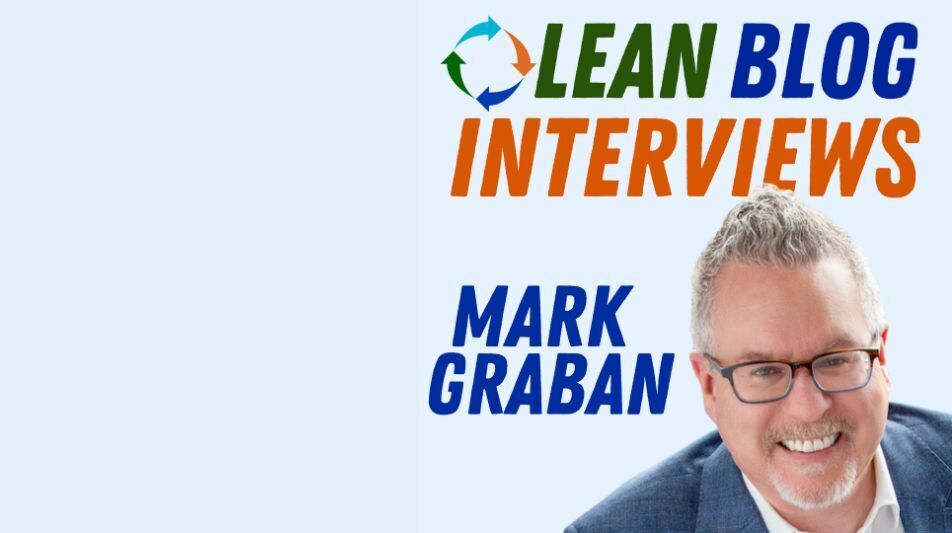
About Mark Graban
Mark Graban is an author, speaker, and consultant, whose latest book, The Mistakes That Make Us: Cultivating a Culture of Learning and Innovation, is available now.
He is also the author of the award-winning book Lean Hospitals: Improving Quality, Patient Safety, and Employee Engagement and others, including Measures of Success: React Less, Lead Better, Improve More.
He serves as a consultant through his company, Constancy, Inc, and is also a Senior Advisor for the technology company KaiNexus.
Mark hosts podcasts, including “Lean Blog Interviews” and “My Favorite Mistake.”
Education: B.S. in Industrial Engineering from Northwestern University; M.S. in Mechanical Engineering, and M.B.A. from the Massachusetts Institute of Technology’s Leaders for Global Operations Program.