Lean Blog Interviews - Healthcare, Manufacturing, Business, and Leadership
Started in 2006, the ”Lean Blog Interviews” podcast, hosted by Mark Graban, brings you conversations with leading experts, authors, and thought leaders in lean manufacturing and management. As a Lean practitioner, consultant, and author, Mark Graban offers deep insights, real-world experiences, and practical tips for implementing and enhancing Lean practices across various industries. The Podcast Experience Mark Graban engages his guests in a conversational format, covering a wide array of topics related to Lean. Guests come from diverse backgrounds, including healthcare, manufacturing, and service industries, sharing their unique experiences and perspectives on Lean implementation. Core Topics Lean Principles and History: Dive into the foundational aspects of Lean, its history, and core principles. Industry Applications: Explore how Lean is applied in different industries, such as healthcare, manufacturing, and startups. Continuous Improvement: Learn about value stream mapping, process improvement, and culture change. Leadership and Management Systems: Gain insights into the Toyota Production System and related methodologies, focusing on Lean as a culture, philosophy, and management system rather than just a set of tools. Unique Features Focus on Healthcare: Mark Graban, a renowned advocate for Lean in healthcare, frequently features experts who discuss patient safety, quality improvement, and waste reduction in healthcare settings. Hear success stories and practical advice on implementing Lean in hospitals, clinics, and other healthcare organizations. Practical Advice and Real-World Examples: Guests share their experiences and insights into what works and what doesn’t in Lean implementation. Overcome common challenges and get inspired by success stories. Inclusivity and Diversity: The podcast features a range of guests from diverse backgrounds, enriching discussions and providing a comprehensive understanding of Lean’s challenges and opportunities. While we don’t talk much about Lean Six Sigma, we hope the podcast is helpful to you anyway. Why Listen? Whether you’re new to Lean or a seasoned practitioner, the ”Lean Blog Interviews” podcast is a valuable resource offering insights, tips, and inspiration for improving your organization’s performance and achieving Lean goals. With its engaging format, practical advice, and diverse range of guests, this podcast is essential for anyone interested in continuous improvement and operational excellence. Connect and Explore More Visit the blog at www.leanblog.org. For feedback, email mark@leanblog.org. Access all past episodes, show notes, and more at www.leancast.org. Subscribe to the ”Lean Blog Interviews” podcast today and join the journey toward Lean mastery and continuous improvement.
Episodes
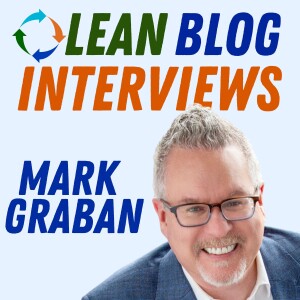
Wednesday Nov 09, 2022
Professor John Grout, a Deep Dive on Mistake Proofing and Lean
Wednesday Nov 09, 2022
Wednesday Nov 09, 2022
Expert on mistakes and mistake proofing, professor and former business school dean
Episode page with video, transcript, and more: https://leanblog.org/462
My guest for Episode #462 of the Lean Blog Interviews Podcast is Professor John Grout the former dean of the Campbell School of Business at Berry College in Rome, Georgia.
He was recently a guest on “My Favorite Mistake” — Episode 186, so I encourage you to check that out.
He's the current Chair of the Technology, Entrepreneurship, and Data Analytics Department and the David C. Garrett Jr. Professor of Business Administration. John has overseen the development, approval and implementation of Berry College's Creative Technologies program and Berry's makerspace, HackBerry Lab.
Dr. Grout has researched mistake-proofing extensively and published numerous articles on mistake-proofing. In 2004, John received the Shingo Prize for his paper, “The Human Side of Mistake-Proofing” with Douglas Stewart. John has also consulted with a large variety of firms to mistake-proof their processes.
He's also published “Mistake-Proofing the Design of Health Care Processes” a book that's freely available online.
His Website: https://mistakeproofing.com/
Today, we discuss topics and questions including:
Your origin story – how did you first get introduced to TPS, Lean, etc? Context of discovering mistake proofing?
Shingo's book on Poka Yoke
“Shingo was not kind to Statistical Quality Control”… use SQC and/or mistake proofing?
Acceptance sampling… keeps bad product out… maybe?
Field goals — Conformity to specs vs. closer to center?
Successive checks and self checks
Source inspections – Shingo's gold standard
Why should you react when a part's out of control but still in spec??
Do you HAVE to stop the line? Don't be dogmatic??
Statistics don't do well with rare events
Do we have data on how universal the “universal protocol” is?
Doctor signing vs. you signing the surgical site?
ZERO – “the only way to go” in terms of goals
The goal of “zero defects” can be controversial.. is it possible? Motivating? Demoralizing?
Possible research – optimal time to stop doing final inspection??
Why is it easier to error proof now? Technology
“People don't like to own up to mistakes”
Naida Grunden episode on aviation safety
Can't error proof everything??
Preventing execution errors is easier than preventing decision errors
The balance and benefits of examples to copy vs. developing thinking?? “Catalog or catalyst”?? BOTH
The podcast is sponsored by Stiles Associates, now in their 30th year of business. They are the go-to Lean recruiting firm serving the manufacturing, private equity, and healthcare industries. Learn more.
This podcast is part of the #LeanCommunicators network.
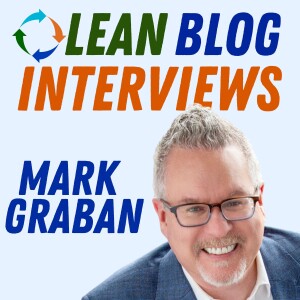
Thursday Oct 27, 2022
Gauthier Duval on Kaizen Events, Organizational Development, and ”Veryable” Labor
Thursday Oct 27, 2022
Thursday Oct 27, 2022
Video, transcript, and more: https://leanblog.org/461
My guest for Episode #461 of the Lean Blog Interviews Podcast is Gauthier Duval, the Director of the Lean Center of Excellence at Veryable.
He's applied and taught Lean for over 18 years, including time with Freudenberg-NOK (an auto supplier featured in the book Lean Thinking), Simpler Consulting, and other manufacturing companies in the U.S. and Europe.
Today, we discuss topics and questions including:
Your Lean origin story?
The next steps in your career and learning??
Freudenberg-NOK — 2004 — Growtth Consulting spinoff
Working with Lean – Europe vs. US?
Simpler – worked with Chris Cooper – Episode #129
Your view on the role of what's often called “kaizens” (kaizen events) vs. ongoing daily kaizen improvement?
Multi-day events vs. small discontinuous improvements?
How should people be participating?
The role of the senior leader?
Kicking a company president out of a Kaizen Event??
Lessons you've learned on the psychology of change?
Organizational behavior and organizational development? — how do you define that?
What makes an organization a “learning organization?”
Chris Argyris — why should more Lean people be reading his work?
Tell us about Veryable – the company, the problems you solve and how it works…
How to expand “JIT” beyond just materials?
Variable labor in a “lean mindset” way — including “respect for people”??
The podcast is sponsored by Stiles Associates, now in their 30th year of business. They are the go-to Lean recruiting firm serving the manufacturing, private equity, and healthcare industries. Learn more.
This podcast is part of the #LeanCommunicators network.
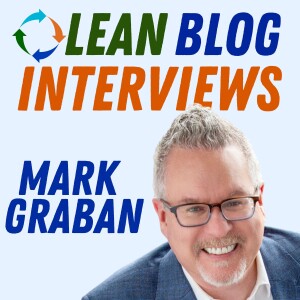
Wednesday Oct 12, 2022
Philip Holt on Leading and Living Lean, With Simplicity
Wednesday Oct 12, 2022
Wednesday Oct 12, 2022
Episode page with video, transcript, and more
My guest for Episode #460 of the Lean Blog Interviews Podcast is Philip Holt.
He is currently Senior Vice President, Operational Excellence at GKN Aerospace, the world's leading multi-technology Tier 1 Aerospace supplier, and has over 30 years of business experience in leadership roles spanning the customer value chain, in industry-leading Companies also including Philips, Gillette, and Travelport.
He is the author of three Lean Leadership books:
Leading with Lean: An Experience-based guide to Leading a Lean Transformation
The Simplicity of Lean: Defeating Complexity; Delivering Excellence
Leading Lean by Living Lean: Changing how you Lead, not who you are
You can learn more at Philip's website.
Today, we discuss topics and questions including:
Your “Lean origin story?”
“Thought I knew what Lean was”
How did visiting Japan help?
Kaikaku — breakthrough improvement vs. continuous improvement
Systemic view of Lean / TPS – can't grab just pieces
True North?? How to define that?
What are some of the ways in which people overcomplicate Lean?
Overcomplicating problem solving? Six Sigma… A3?
Start at the most simple form of problem solving
How do you describe Lean simply?
How do you define “transformation”? When it's fully aligned with the strategy of the company…
What “transformational results” would you expect to see?
Zero Accidents goal – the Heinrich Triangle
Unlearning the old way so we can lead in a Lean way?
The personal benefits of Lean at work and life??
What is a “life in balance”?? What does that mean to you?
Using lean tools at home?
Push vs. pull for information??
The podcast is sponsored by Stiles Associates, now in their 30th year of business. They are the go-to Lean recruiting firm serving the manufacturing, private equity, and healthcare industries. Learn more.
This podcast is part of the #LeanCommunicators network.
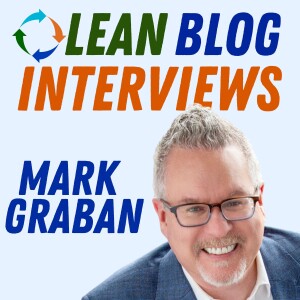
Tuesday Oct 04, 2022
Tuesday Oct 04, 2022
VP of Advisory Services, Value Capture
Episode page with video, transcript, and more
My guest for Episode #459 of the Lean Blog Interviews Podcast is my colleague, Gerald Harris, a Vice President of Advisory Services at the firm Value Capture.
Disclosure – I often work as a senior advisor with Value Capture clients and I have a marketing role with the firm.
Gerald has over 25 years of leadership experience in the delivery of successful large-scale lean transformations across a broad range of industries and companies. His industry experience includes various automotive manufacturing settings and products and, for the past 14 years, healthcare.
While at Tenneco Automotive, a $1.5 billion manufacturer of exhaust and ride control systems, Gerald implemented lean manufacturing and lean enterprise improvement principles throughout the organization.
For the 14 years before joining Value Capture, Gerald served as Executive Director for Simpler North America, where he was instrumental in client launches and Executive Coaching for most of Simpler's largest clients.
Today, we discuss topics and questions including:
How — when and where — did you first get introduced to Lean?
Motivations for Lean in those early settings?
Early activities — what went well? Lessons learned from challenges?
PULL – “flow if you can, pull if you must, but never push”
Did people there even think that improvement was possible? Any improvement was possible?
Short-term vs. longer-term countermeasures, adding inventory to be able to improve — or adding labor?
“Step change” – response to medication errors? Adding inspection step?
Interesting that Toyota still has final inspection??
Systems vs. processes?
Work, management, improvement systems
From nursing tasks to the healthcare value stream
Seeing vs. purposeful observation?
Value Capture's “guided self-assessment”
Leaders being too far removed from the work in healthcare
How did you find the right balance as a plant manager?
You've gotten more than comfortable with both… Bigger adjustment — becoming a consultant or shifting into healthcare?
The pitch for Value Capture?
Envisioning the IDEAL – how do we get to zero?
The podcast is sponsored by Stiles Associates, now in their 30th year of business. They are the go-to Lean recruiting firm serving the manufacturing, private equity, and healthcare industries. Learn more.
This podcast is part of the #LeanCommunicators network.
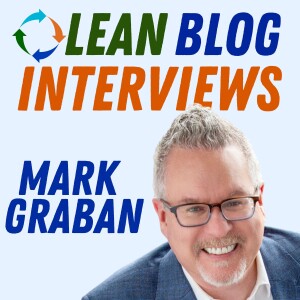
Wednesday Sep 28, 2022
Damon Baker on Lean, Private Equity, and the Ownership Works Initiative
Wednesday Sep 28, 2022
Wednesday Sep 28, 2022
Partner with Coltala Holdings
Episode page with video, transcript, and more
My guest for Episode #458 of the Lean Blog Interviews Podcast is Damon Baker. He was recently my guest in Episode #454.
He is the founder and CEO of the firm Lean Focus. He's also a Private Equity Partner at Coltala Holdings.
Today, we're taking a deeper dive into the world of private equity, how Lean can support a particular P.E. model, and the “Ownership Works” Initiative.
Damon Baker has been implementing Lean practices in various GM & VP-level capacities for more than 25 years, but it was at Danaher, where he worked for nine years, that his passion for true business transformation was born. He was instrumental in developing Danaher's company-wide Problem-Solving Process, and was inspired to create a new, comprehensive business system that enables organizations to improve on all fronts.
He has worked in a Shingo Prize-winning facility and is a Shingo Prize Examiner.
Over his career, Damon has demonstrated hands-on leadership and facilitation of 500+ kaizen events in close to 100 major corporations in 16 different countries.
Today, we discuss topics and questions including:
Private Equity 101?
Public vs. private vs. private equity?
Two types of P.E. firms
Time is up and the fund exits? Means they have to sell the companies?
Has there been a shift in the PE philosophy on extracting value vs. creating value, or do some just do it differently / better?
Mission over margin? Conscious Capitalism?
Lean in private equity — What does PE care about?? Vs. Public Equity
How did you get first get involved with PE?
Coltala Enterprise System? Which tools to apply in which business? Priorities and problem solving?
A lean practitioner working for a PE-owned company? What to ask or look for?
Humility and confidence – Larry Culp talked about this
Tell us about the “Ownership Works Initiative” — KKR and other firms (TPG) – it's not ESOP model
The podcast is sponsored by Stiles Associates, now in their 30th year of business. They are the go-to Lean recruiting firm serving the manufacturing, private equity, and healthcare industries. Learn more.
This podcast is part of the #LeanCommunicators network.
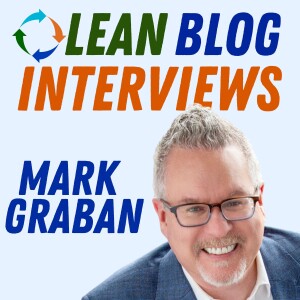
Wednesday Sep 21, 2022
Wednesday Sep 21, 2022
Kata geek and coach
Episode page with video, transcript, and more
Joining me for Episode #457 of the Lean Blog Interviews Podcast is Sam Morgan.
Sam is a self-proclaimed “confident learner” and earlier this year after 5 years of practice in the continuous improvement space he landed at KataCon, a conference for continuous improvement professionals who practice the Toyota Kata.
At KataCon, he had a powerful moment realizing where his true passion lies: transforming people through coaching. I'll ask Sam more about that. Sam finds joy in seeing his clients move from fearful to fearless; from insecure to confident.
I know Sam as the host of the YouTube series “C.I. in 5” and he's been part of a learning and collaboration group called “The Lean Communicators.“
His newly launched coaching website is www.illuminatecoach.com. You can also find him on LinkedIn.
Today, we discuss topics and questions including:
How, when, and where did you first get introduced to continuous improvement concepts and methods?
How did you get introduced to Toyota Kata?
What does it mean to be a “confident learner”?
Adam Grant's book Think Again
Why “Sam Loves Lean” as an email account and account name?
We turn the tables on Sam to ask him his “C.I. in 5”
What is your C.I. in 5? – “confident learning for all”
Tell me about your t-shirt… and for those who are listening via podcast instead of watching via YouTube
Respect for people
Intentionally focusing on inviting guests who are women of color? And people of color more broadly…
“There's not that many Black faces in attendance at Lean conferences, yet alone up on stage,… in what way does systemic racism cause that? What can we, what should we do about that?”
Being welcoming vs. expanding the pool?
Company representation in CI roles?
What is your “Illuminate U” program?
The podcast is sponsored by Stiles Associates, now in their 30th year of business. They are the go-to Lean recruiting firm serving the manufacturing, private equity, and healthcare industries. Learn more.
This podcast is part of the #LeanCommunicators network.
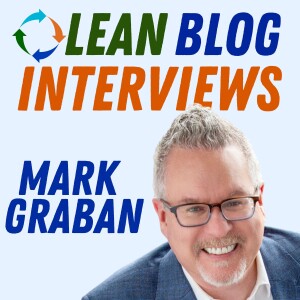
Wednesday Sep 14, 2022
Wednesday Sep 14, 2022
CEO of Stiles Associates
Episode page with video, transcript, and more
Joining me for Episode #456 of the Lean Blog Interviews Podcast is Jake Stiles, CEO of Stiles Associates.
For nearly three decades, Jake has played an instrumental role in growing Stiles Associates from a niche recruiting agency to the premier Lean executive search firm in the country.
He's helped transform client organizations by placing top talent across a wide spectrum of industrial segments including manufacturing, consulting, healthcare and professional services.
As Lean and continuous improvement have spread from factory floors to hospitals, financial institutions and beyond, Jake has continued to build ties to thought leaders and increase Lean's scope at the most innovative institutions.
As a result, he's served as a member of numerous industry associations and boards – including the Association for Manufacturing Excellence (AME) and the Greater Boston Manufacturing Partnership (GBMP).
Disclosure: Stiles Associates has been a sponsor of the podcast since the start of 2021.
Today, we discuss topics and questions including:
How did you first get introduced to Lean?
Brought Art Byrne into Wiremold as CEO
Looking for 80% personality / 20% technical??
“Not settling… always pushing, but bringing the team along” — emotional intelligence
Tips for being successful in a new environment?
Transformational executives? Does their experience translate?
Operating vs. transforming – how to evaluate beyond a willingness to lead it??
Search process similar to the transformation process — understanding the current state and the issues… what problem are you trying to solve? Iteration with the client
Jumping across industries — in particular Manufacturing to Healthcare? Key success factors?
How are you counseling hiring companies in a very competitive market?? Candidate-driven market?
Advice for how to work with a recruiter (as a candidate) vs. applying directly for a job?
Compensation “correction” is coming??
Is accepting a counteroffer always a bad idea?
Differences in working for a public company vs a PE company?
The podcast is sponsored by Stiles Associates, now in their 30th year of business. They are the go-to Lean recruiting firm serving the manufacturing, private equity, and healthcare industries. Learn more.
This podcast is part of the #LeanCommunicators network.
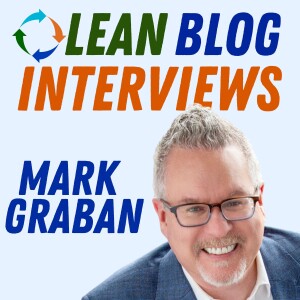
Wednesday Aug 24, 2022
Ken Pilone, the Author of Lean Leadership on a Napkin; Toyota Says ”Lean” and More
Wednesday Aug 24, 2022
Wednesday Aug 24, 2022
Former Toyota employee and author
Episode page with transcript and more
My guest for Episode #455 of the Lean Blog Interviews Podcast is Ken Pilone. He is the author of Lean Leadership on a Napkin: An Executive's Guide to Lean Transformation in Three Proven Steps.
Ken has more than 30 years of experience in Organization Development in Government, Retail, Automotive, Distribution, and Aerospace. He is currently the Senior Manager of Business Process Engineering at Providence Health & Services — a role that encompasses internal Lean consulting, including executive coaching, lean training, leadership development, and all functions typical of a lean promotion or PI/CI function.
He spent nearly 20 years with Toyota as Lean consultant within company as well as with suppliers, vendors, partners and community groups. He a co-creator of the University of Toyota at the company HQ. He led the work to adapt the Toyota Production System to non-production environments (warehousing, supply chain, HQ administration depts., sales, product distribution, dealer operations, etc. In addition, he led the Center for Lean Thinking.
Ken has a Masters in Industrial Psychology and Organizational Development with his Toyota experience, Ken has developed specialties in Lean consulting in non-production environments, curriculum development and delivery, leadership and management development coaching, Toyota problem solving method training and public speaking.
Today, we discuss topics and questions including:
Your Lean/TPS origin story?
How did you end up at Toyota?
How did they train and develop you?
What did you have to unlearn?
The University of Toyota – purpose for that?
Bigger challenge: Translating TPS and Japanese where it's not manufacturing or where it's not Japan?
The “Center for Lean Thinking” at Toyota — No heartburn over the word Lean? Why call it that? Was there debate about that?
“The Toyota salute” = a shrug (I dunno)
TPS = Lean? It depends??
Hard to get Toyota to define TPS — always changing
How was Toyota distinguishing between TPS and Lean internally?
Copying practices vs. principles?
“Single biggest failure mode” = practices & tools and why aren't I getting the same result…
“Toyota Traditions” curriculum
What inspired you to write the book?
3 step approach — introduction, integration, and internalization? Vs. implementation?
The most common or most harmful misinformation out there about Lean and Lean leadership?
5 Whys — why 5 isn't a “rigid rule”?
Why could it be seen as “offensive” if somebody describes themselves as a “sensei”?
The podcast is sponsored by Stiles Associates, now in their 30th year of business. They are the go-to Lean recruiting firm serving the manufacturing, private equity, and healthcare industries. Learn more.
This podcast is part of the #LeanCommunicators network.
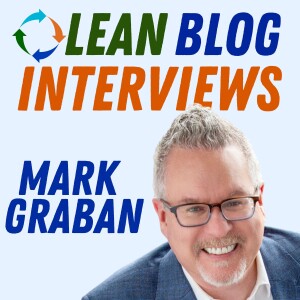
Tuesday Aug 16, 2022
Tuesday Aug 16, 2022
CEO of "Lean Focus"
Episode page with video, transcript, and more
My guest for Episode #454 of the Lean Blog Interviews Podcast is Damon Baker. He is the founder and CEO of the firm Lean Focus. He's also a Private Equity Partner at Coltala Holdings.
Damon Baker has been implementing Lean practices in various GM & VP-level capacities for more than 25 years, but it was at Danaher, where he worked for nine years, that his passion for true business transformation was born. He was instrumental in developing Danaher's company-wide Problem-Solving Process, and was inspired to create a new, comprehensive business system that enables organizations to improve on all fronts.
He has worked in a Shingo Prize-winning facility and is a Shingo Prize Examiner.
Over his career, Damon have demonstrated hands-on leadership and facilitation of 500+ kaizen events in close to 100 major corporations in 16 different countries.
Today, we discuss topics and questions including:
How did you first get introduced to Lean or TPS — what was the context and the circumstances?
Want people to have a positive experience with Lean…
Evaluating someone's lineage?? Company, influences, who they learned from??
What were the key components of the Danaher Business System — and why a “business system” instead of a “production system”?
You say “The Lean community has a marketing problem” — why is that and how do you define that problem?
Our language vs. the language CEOs speak
CEOs care about value creation, making the quarter, how Lean is going to help them
Conferences as echo chambers — where are CEOs and CHROs going to?
“Our CEO isn't buying in…” — what do you suggest?
How many CEOs are “Lean Zealots” like Art Byrne??
Tell us more about your firm Lean Focus –what types of clients do you serve?
Lean in private equity — What does PE care about?? Vs. Public Equity
Has there been a shift in the PE philosophy on extracting value vs. creating value, or do some just do it differently / better?
Tell us about the “Ownership Works Initiative” — KKR and other firms (TPG)
The podcast is sponsored by Stiles Associates, now in their 30th year of business. They are the go-to Lean recruiting firm serving the manufacturing, private equity, and healthcare industries. Learn more.
This podcast is part of the #LeanCommunicators network.
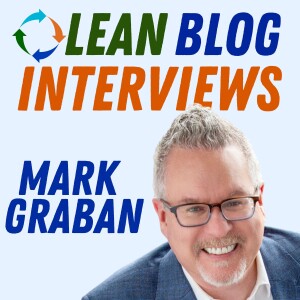
Tuesday Aug 09, 2022
Tuesday Aug 09, 2022
My guest for Episode #453 of the Lean Blog Interviews Podcast is Sarah Boisvert. She is the founder of New Collar Network and Fab Lab Hub.
Episode page
Her career spans advanced “smart” manufacturing, art and music, and innovative workforce training.
Her mission as part of the Fab Lab Network is to create pathways that often do not require college degrees to well-paying, engaging “New Collar” careers, utilizing disruptive technologies like 3D printing, laser machining, robotics, VR and AI/machine learning.
She's joining us on the podcast from Albuquerque.
She is the author of the books The New Collar Workforce and People of the New Collar Workforce.
In collaboration with Santa Fe Community College, Boisvert also founded the New Collar Innovation Center at the Santa Fe Higher Education Center in 2021 to foster innovation in lifelong learning, New Collar workforce training, and the creation of 21st-century startups.
Sarah is going to be part of a main stage keynote panel at the AME annual conference, being held in Dallas, October 17 to 20.
Joining Sarah on the panel are Deondra Wardelle, who was my guest in Episode 405, and also Amy Gowder, President and CEO of GE Aviation Military Systems Operations. I'm going to be moderating the panel.
Today, we discuss topics and questions including:
You've done many fascinating things in your career… but to ground the conversation, for this podcast, what was your first exposure to Lean manufacturing?
Deming?
Lean in your kitchen?– her choice, reducing frustration
“Lean is people centric”
You said in 2018: “U.S. manufacturing companies are expected to face a shortage of 2 million skilled workers by the year 2020.” — assume this came true? Made worse by the pandemic?
It's worse, much worse than predicted?
A problem beyond manufacturing
For these new technologies…Which of those skills are most in short supply?
What are the skills that “new collar” employees need to have… coming out of high school?
Problem solving — it CAN be taught
As you shared on LinkedIn… “General Motors is expanding hiring requirements to skills, not just degrees!
Give an example of how “degree creep” causes problems?
Working with Los Alamos National Laboratories to also change hiring policies?
As an expert in 3D printing, how do you help companies decide when 3D printing isn't just “cool” but is actually more effective and the preferred choice?
Are your earrings 3d printed? YES
What are the benefits of 3D printing??
There are people in Dallas working on a 3D-printed house? Concrete?
The podcast is sponsored by Stiles Associates, now in their 30th year of business. They are the go-to Lean recruiting firm serving the manufacturing, private equity, and healthcare industries. Learn more.
This podcast is part of the #LeanCommunicators network.
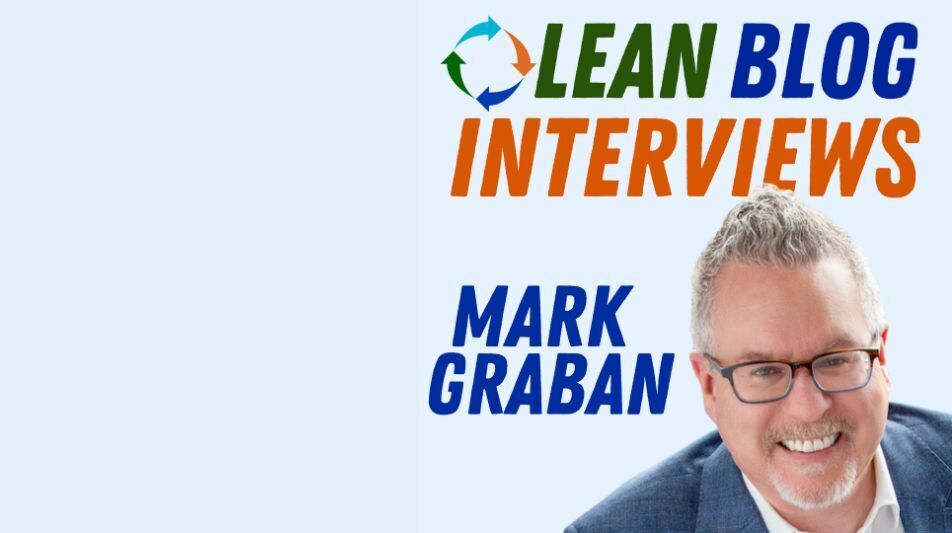
About Mark Graban
Mark Graban is an author, speaker, and consultant, whose latest book, The Mistakes That Make Us: Cultivating a Culture of Learning and Innovation, is available now.
He is also the author of the award-winning book Lean Hospitals: Improving Quality, Patient Safety, and Employee Engagement and others, including Measures of Success: React Less, Lead Better, Improve More.
He serves as a consultant through his company, Constancy, Inc, and is also a Senior Advisor for the technology company KaiNexus.
Mark hosts podcasts, including “Lean Blog Interviews” and “My Favorite Mistake.”
Education: B.S. in Industrial Engineering from Northwestern University; M.S. in Mechanical Engineering, and M.B.A. from the Massachusetts Institute of Technology’s Leaders for Global Operations Program.